SpeedyXY 3D Printer
Why Design Another Printer?
First and foremost, I designed SpeedyXY because I wanted to. I think it's hard to deny you learn a lot more build than buying. That said, there were a few specific features I wanted that are pretty uncommon on consumer machines.
The Extruder
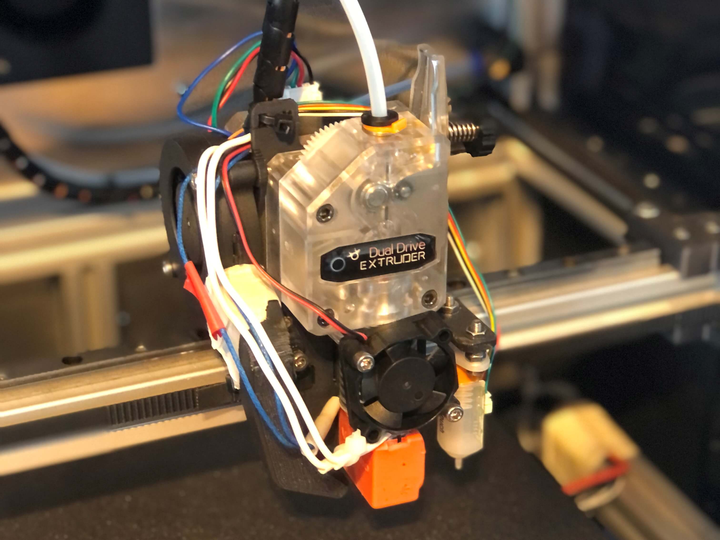
Firstly, I wanted a direct-drive extruder. An extruder is usually a stepper motor with a set of toothed gears. Its job is to get the plastic filament feed-stock from the spool to the entry of the hotend (which melts and deposits it). Most commercial printers mount the extruder in a fixed location on the frame of the printer, and run a "Bowden tube" to the printhead. This is usually good because it keeps the moving mass of the printer low, but there are downsides. The first problem is that the Bowden tube introduces slop, as the filament can deflect against the walls of the tube. This can make maintaining very precise control of the plastic flow difficult, especially when the flow rate is changing rapidly (like when printing very small disconnected features). The second issue is more significant. When printing certain flexible plastics (like TPU, or Thermo-Plastic Urethane) the filament can actually get stuck in the Bowden tube, ruining a print. The solution to these problems is a direct-drive extruder, which is mounted directly onto the print head. This eliminates the need for a Bowden tube, and makes it much easier to print flexible filaments. This leads to a much more versatile machine that is useful for a wider range of projects.
The Mechanics
One of the reasons many consumer printers don't use a direct-drive extruder is because of the significant additional moving mass it introduces. In general the print head weighs at least twice as much as in a Bowden configuration. This weight is an issue because when the printer moves, particularly at high speeds, it starts to vibrate. In the absence of a better model we can pretend the printer is a mass-spring system. The resonant frequency of the kinematic assembly is then proprotional to the square root of the stiffness-mass ratio. As the stiffness decreases or the printhead mass goes up the normal forces of printing can come closer and closer to exciting the natural modes of the structure. Luckily, this isn't a high-school physics class and the printer isn't a bridge so it probably won't fall apart, but the print quality can decrease drastically. Given that the print head is going to be heavier with a direct-drive system, we need to either slow down (and excite the structure less), or make the structure stiffer (and increase its natural frequency). Slowing down isn't any fun, so I chose to build stiffer. SpeedyXY has an aluminum frame made of 2020 extrusions, and sheet-metal panels on nearly all sides. The main purpose of these panels is to enclose the printer, but they also help stiffen the structure in a way that most consumer printers lack.
Text in progress